試作から量産、開発段階からあらゆるプロセスで課題解決を支援
樹脂切削
要求仕様の満足&不良予測…
樹脂屋視点から最適スペックを追求
薄肉や厚肉、小径、通気、絶縁などハイエンド製品や特殊用途の製品に関するご相談は、樹脂の要求仕様に対して提案を心がけております。それに比例して成形の難易度が高まるケースが多々あります。時にはお客様の多様な要求仕様に対し、樹脂屋の視点の見地から考え、多彩な工法の提案やこれまでのエラーの歴史から学んだノウハウにより最適スペックの追求を支援します。
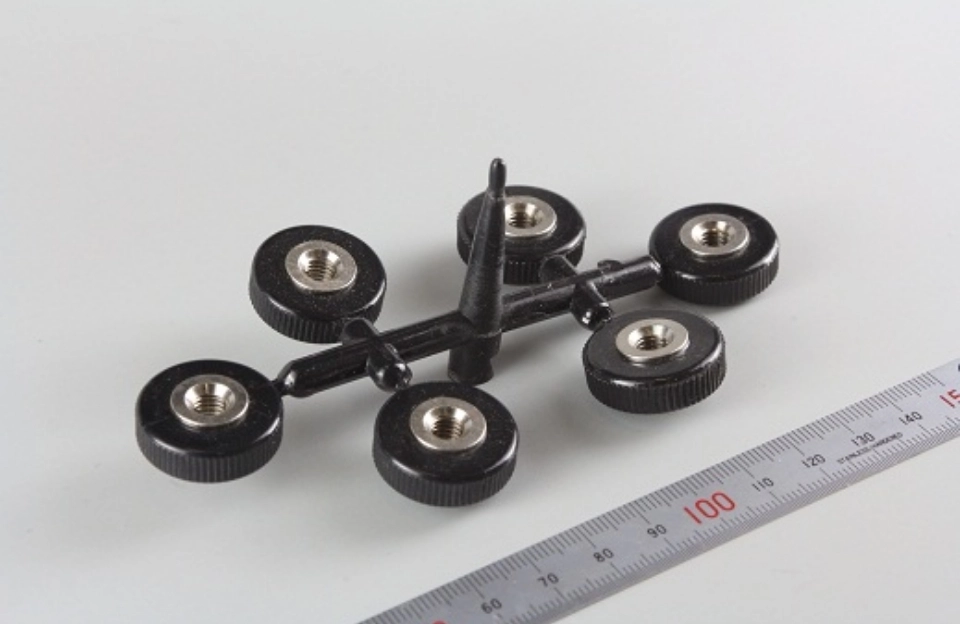
要求仕様
金型成形or金型レス…
“型”に捉われず最適コストを追求
数十個~数百個の樹脂製品は、形状・材質・ロット・デリバリーなどの違いにより最適な工法は異なるため、金型成形と金型レス、両方のアプローチが必要になります。弊社では長年の経験を活かした技術が、お客様の要求仕様に応じた最適な工法を提案します。
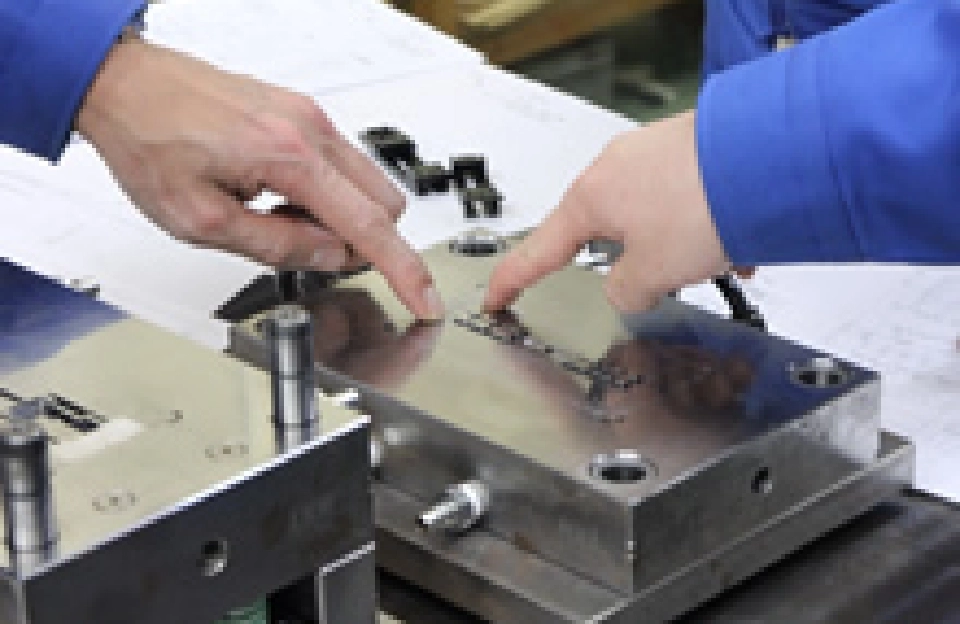
商品化・樹脂初心者
最小スタートvs.生涯ロット…
お客様視点からアイデア実現を支援
新機軸の製品開発や、市場投入を目的とした新商品のリリースなど、開発初期のご相談では、特に小ロット生産が役立ちます。それに伴い、生産数の見通しを立てると、難易度が高い工法を選択してしまうケースが多くあります。弊社では、最小スタートと生涯ロット製品の生産を両立させる最適な工法提案とリードタイム短縮、リスク分散を目的としたデュアルソーシングのカバーなど、アイデア実現の動きを支援します。
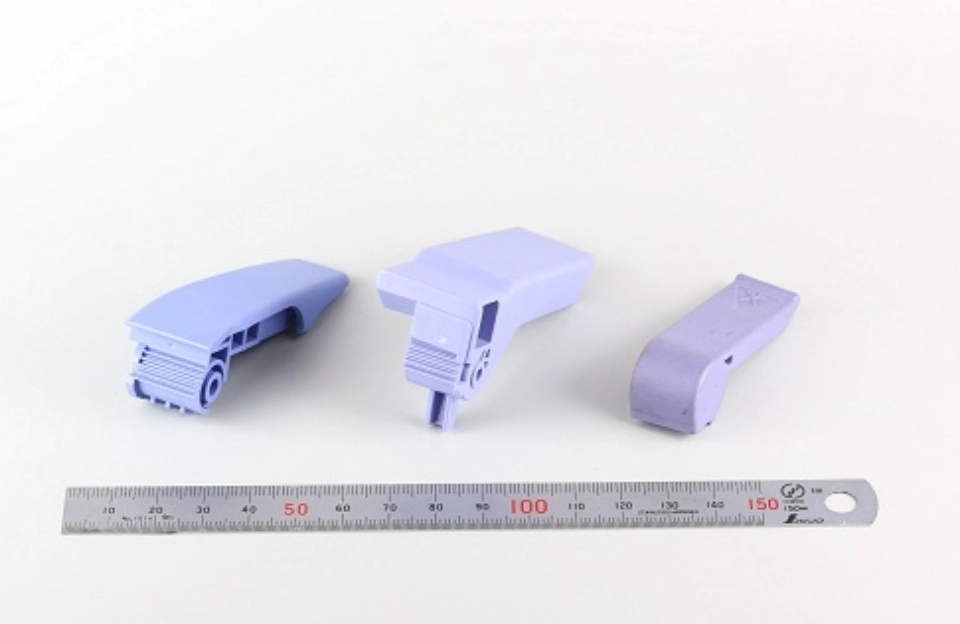
あらゆるプロセスで課題解決を支援
試作(少ロット生産)
設計 | デザイン / 3D設計 / 3Dスキャン 自動機設計(生産技術) |
---|---|
3Dモデリング | FDM(熱溶融積層造形) シリコン型 注型 |
切削加工 | 樹脂切削(マシニング) 金属切削(※金型部品の加工) |
量産(成形技術)
熱可塑性樹脂 | 射出成形 |
---|---|
熱硬化性樹脂 | 圧縮成形 コンプレッション成形 トランスファー成形 射出成形 注型 FRP巻取成形 |
※全工法にてインサート成形 & 組立に対応
みづほ合成の開発支援事例
樹脂成型のさまざまな課題解決を支援する経験と実績
多様なアプローチで問題検証に取り組み、
素早く深いトライ&エラーで開発を支援します
case1課題
熱硬化性樹脂の折損対策
製品 | 消弧棒 |
---|---|
材質 | ユリア樹脂(UF) |
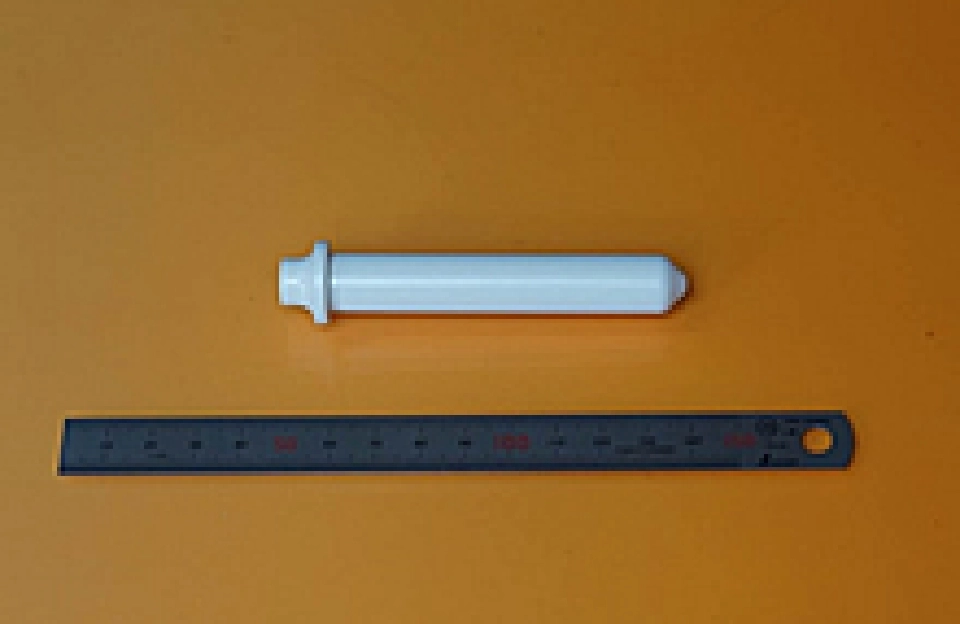
case2課題
コイルインサートの変形対策
製品 | ローター |
---|---|
材質 | ポリフェニレンサルファイド(PPS) コイルインサート |
ステッピングモーターの心臓部。このコイルが曲者で射出圧力に負けて変形してしまい、ほとんど不良というところからスタートしました。
成形条件を可能な限り低圧射出で、金型温度を出来るだけ高く保ち変形を止めようとしましたが上手くいきません。徹夜まがいで当時の工場長が試行錯誤しているうちに、ある工程でとんでもない間違えを気づかずにそのまま成形。何と、それが良品に!!
良品が急にできるようになったのはいいのですが間違えに気づいていないので、なぜ良品が可能になったかさっぱりわからず2日悩みましたが…。ついに気が付いて間違えを再現!
結局それは間違えではなく新たな対処法となったのでした。
ちょっと笑い話ですが、ほんの少しの変化を注意深く分析して得られた貴重な経験でした。
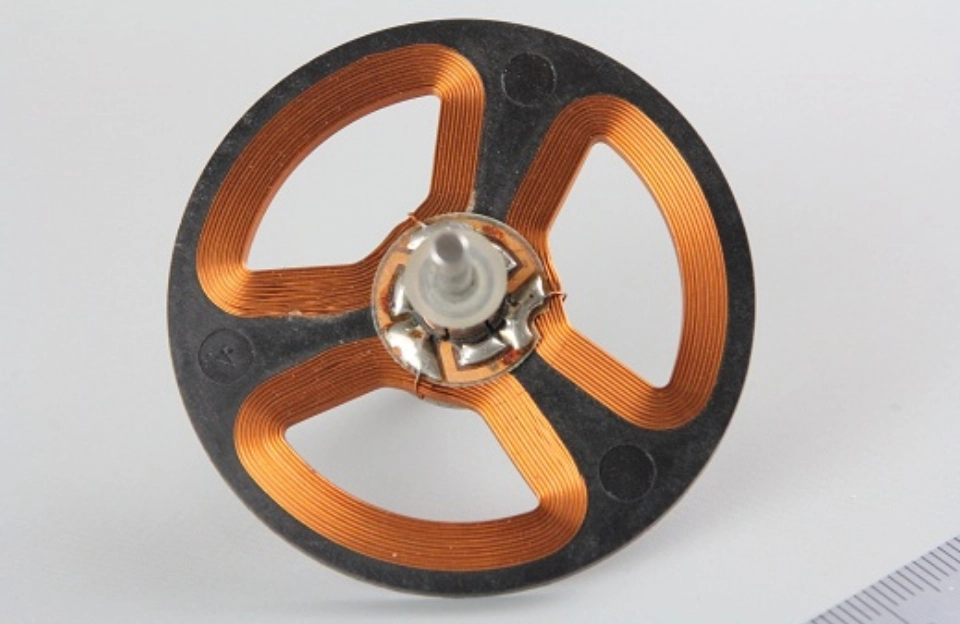
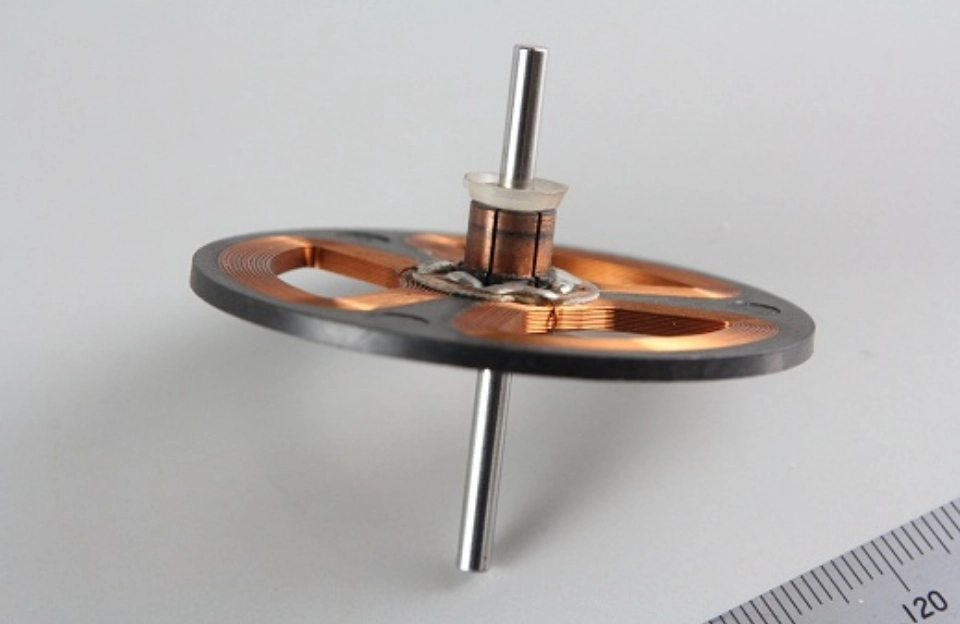
case3課題
ファン形状の重量バランス調整
製品 | FAN & ラジエターファン |
---|---|
材質 | 6,6ナイロン ガラス入り(PA6.6+33%GF) ポリプロピレン ガラス入り(PP+30%GF) |
私が入社して最初に課題にさせられたのがこれでした。(真っ直ぐな羽のFAN)
FAN全体のアンバランスを最終的に金型で調整します。要はタイヤに鉛の重りをつけてバランスを取るのと同じで羽の厚みを変えて重量バランスを取ります。
でも30年ほど前はそれほど金型精度もよくなく、またバランス量を計算して金型を直すのですが、取りすぎたり、少なかったりで、何度も金型を削りなおしてバランスを取るのが常でした。それを根本的に解決するような金型構造に思い切って変更!これで私はバランス取りの名人になれました。
その後は3D形状のラジエターファンでもその経験を活かし、バランス取りを含めた量産の立ち上げも短納期での対応を可能としました。
現在はバランス検査機も所有し品質管理にもしっかり対応します。
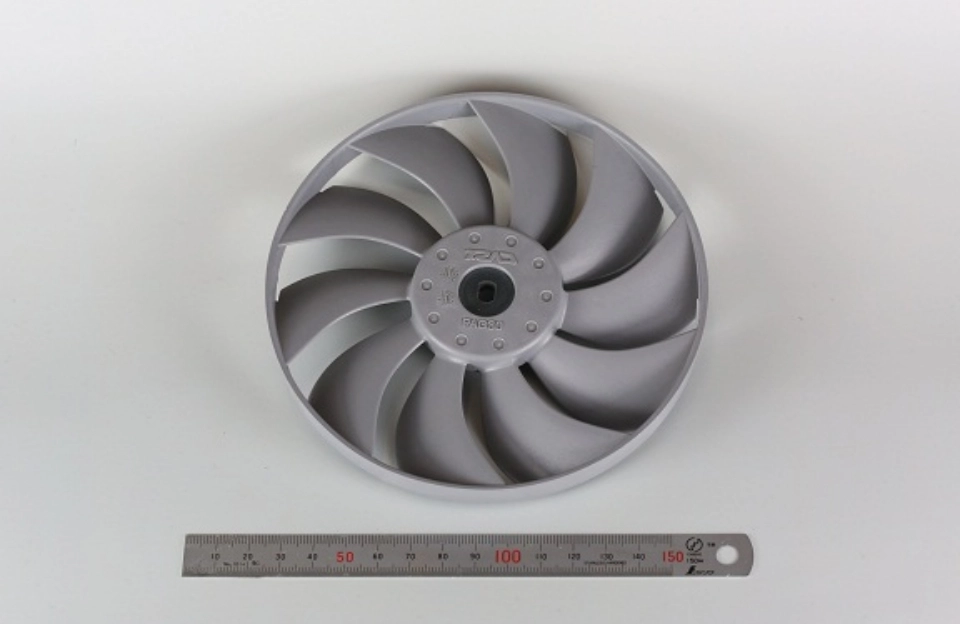
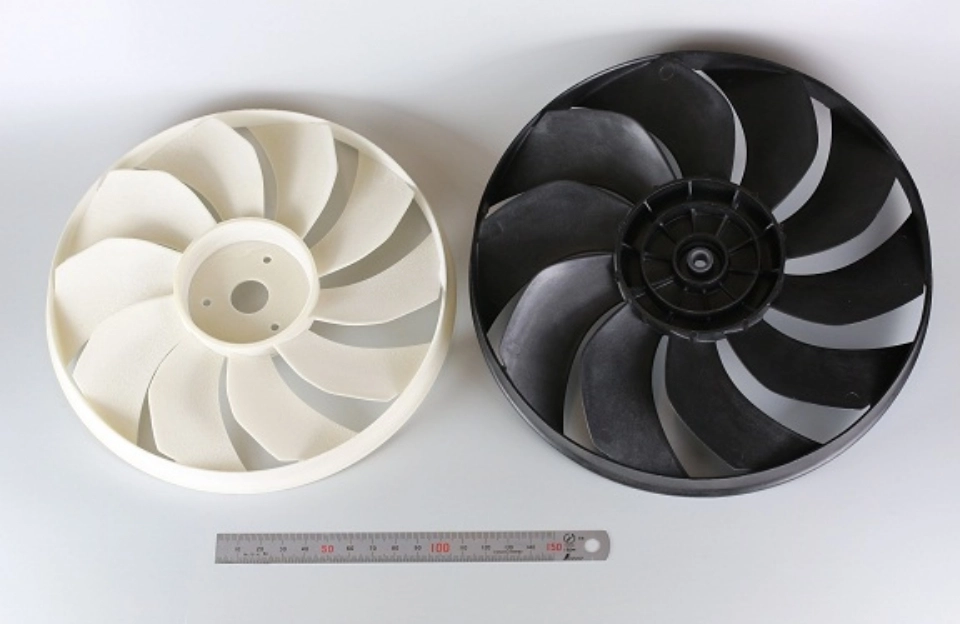
case4課題
熱硬化性樹脂インサート成形品
極肉厚の反り対策
製品 | 高電圧用端子 |
---|---|
材質 | エポキシ樹脂(EP) インサート |
6600Vの送電線からの1次線や200Vへの変換後の2次線を支える極肉厚の熱硬化性樹脂のインサート成形です。非常に簡単な形状ですがこれを0.1mm以下の平面度を保って真っ直ぐな製品を得ることは結構難しいものがあります。材料の収縮、金型温度の分布、材料の流動性、等々…不安定要因満載ですが、基本に立ち返り、当社得意のコンプレッション成形(圧縮成形)と金型構造でこれを解決!
解決までは、反りを矯正治具で逆方向に力を掛けてアニーリングしたりして不良を出しながらの対処療法のような生産をしていましたが、今は全てが良品です。
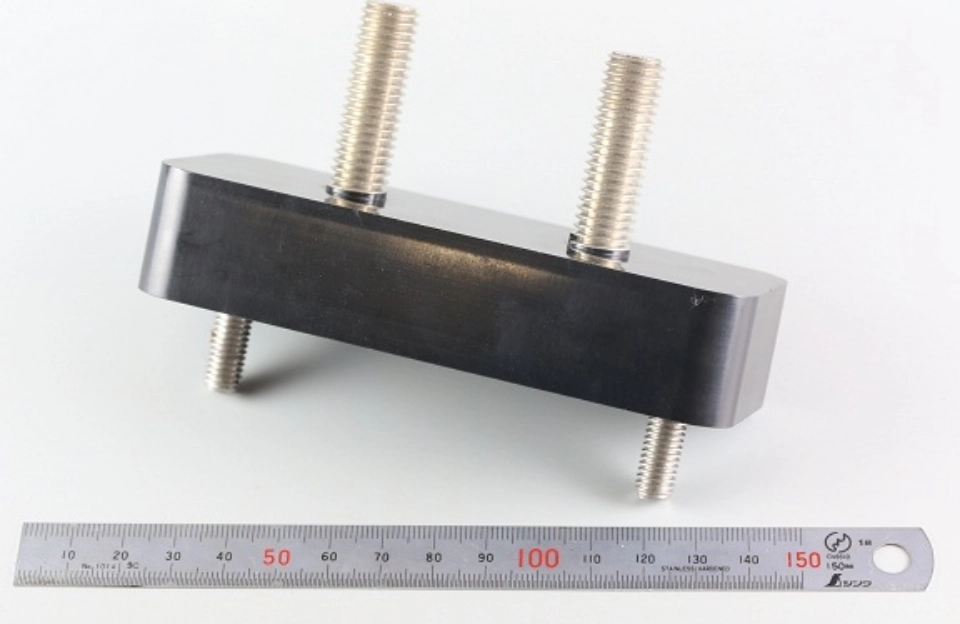
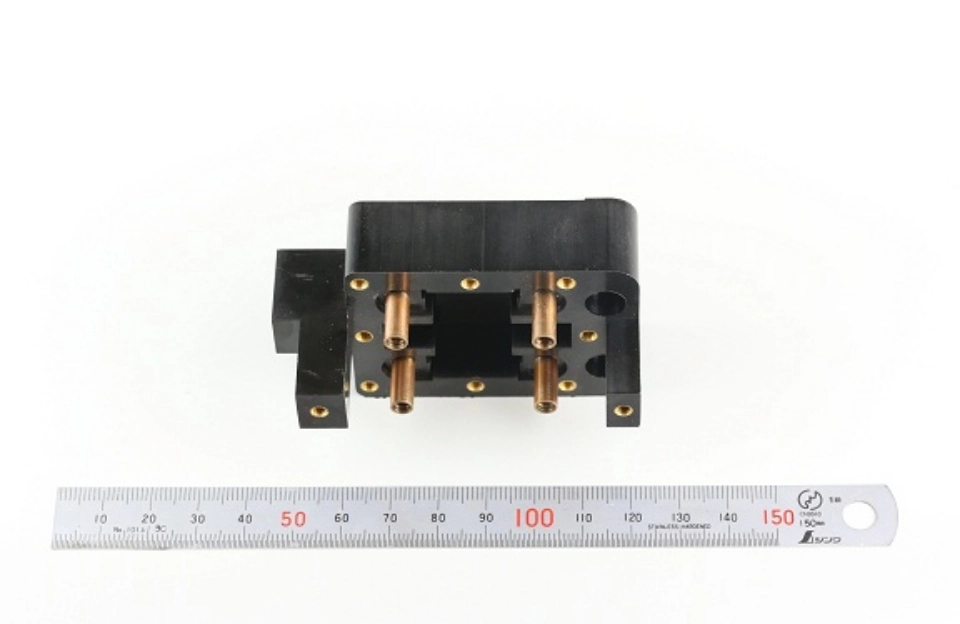
case5課題
難燃グレードのデラミネーション不良対策
製品 | インバーター用ケース(本体・操作パネル等一式) |
---|---|
材質 | ポリフェニレンエーテル(PPE) ポリフェニレン(PPO) |
デラミネーションという不良をご存知でしょうか?
一見製品は綺麗に見えるのですが、実は中が空洞化してしまい物性特性が全く落ちてしまっている状態です。酷いものは水ぶくれのように表面が膨れ上がり、まるで形の悪い醤油せんべいのような状態になってしまいます。
さらにこの不良は成形直後に起こらず、数時間後に起こるから大変恐ろしい不良です。
私は韓国でTRYを行い、喜んでハンドキャリーで30セットのサンプルを日本へ持ち帰り、翌朝サンプルを納品しようとしたら全て不良!すぐに韓国へ飛んでやり直す・・・でも上手くいかない。とんだ目に会い苦い経験をしたものです。
結果的には成形条件・金型の変更で見事不良ゼロに落ち着くことができました。
UL規格のV-0のように難燃グレードの材料には少なからずこの不良を考慮しておかないと痛い目に会うので難しいところです。
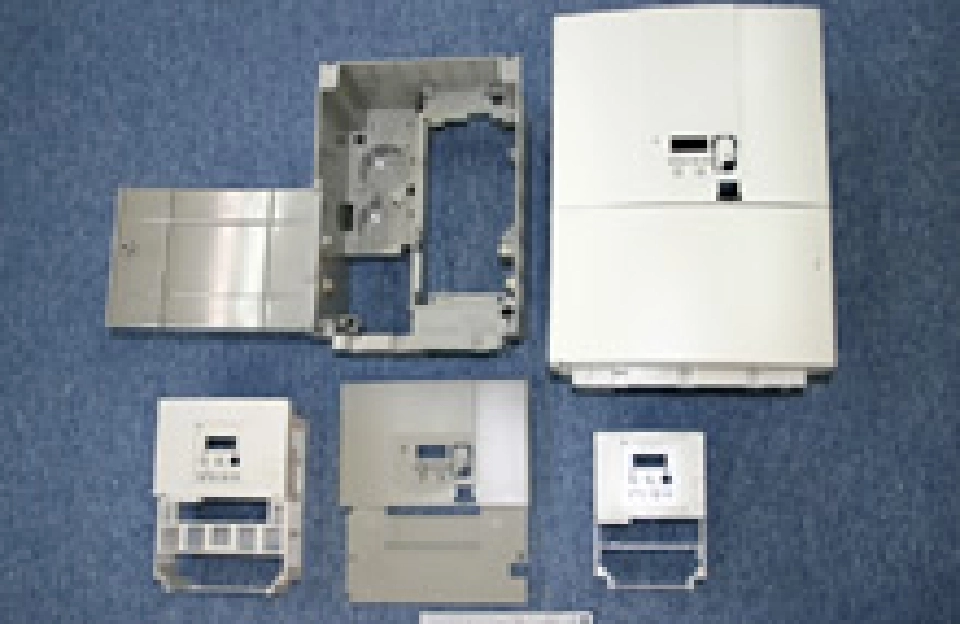
長さ90mm/直径φ15mmの単純な形状ですが、この製品が1~2年に一度、真ん中から真っ二つに折れてしまう不良が必ず起こりました。(年間生産量3~5万個)
最初は原因がわからずにずいぶん悩みましたが、成形方法をトランスファーからコンプレッションへ、さらに材料の投入方法、成形周辺機器の自動化を施すことで、不良率ゼロ・低コスト化の実現に成功しました。
熱硬化性樹脂の成形方法のアプローチは60数年に渡る当社のノウハウが最適な方法を提供します。